智能制造发展的重要议题之一就是让制程中各类的设备进行联网,将运作状态传送至上位系统进行储存、运算与分析,让管理者可通过数字化平台实时掌握制造现场信息。但设备通讯联网涉及的层面广,未经整合的信息传输与数据分析,会使上位机系统工作负担过大,反而影响系统的整体效率,这也是智能制造发展过程中的痛点之一。如何有效率的将智能制造导入自身工厂,是智能制造的首要问题。
近日,台达推出的整线自动化管控系统DIABCS (Block Control System),成功导入某电动车客户,为其打造更迅速、更高效的产线制程控制与管理。
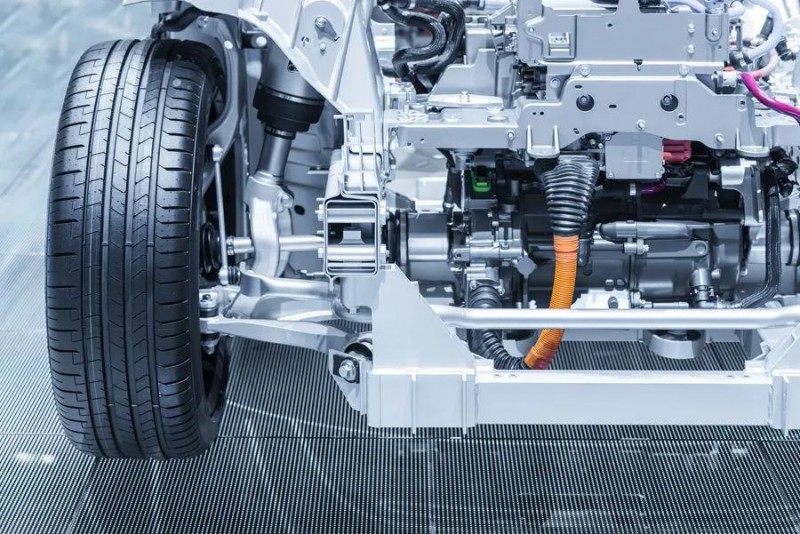
客户生产线上约有80台设备,主要用于制造车用电机。因为设备由多个设备厂商提供,控制器通讯方式没有整体规划,导致信息不能互通,只能进行单一机种的生产。同时,生产物料需通过人员手动刷取条码确认生产制程,再人工选择机种配方后才能进行生产,常常出现因产线人员经验不足而影响投产的效率,功能需求无法客制化,产线建置时间过长。另外,车间现场不能获取产线信息,需通过制造执行系统MES 追溯取得制程数据,而且没有自动备份机制,系统发生问题会导致产线停摆,影响制程效率和产能。
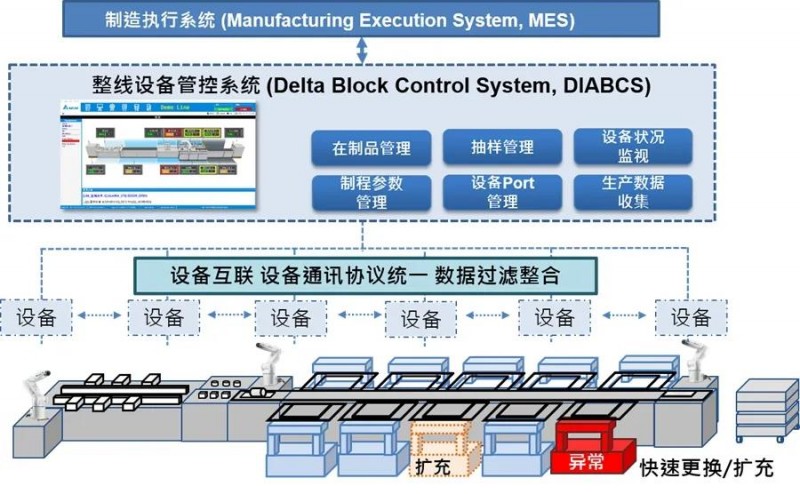
针对这些状况,台达通过成熟的整合技术,为客户导入台达DIABCS整线设备管控系统。该系统位于智能制造中设备联网与上位系统的中间层,纵向串联工厂设备及上层制造执行系统间的数据流,整合工厂内自动化设备与工作站,对下负责设计产线设备的运作流程,对上则以单一通讯协议与MES连接。通过设备互联汇整数据流与边缘计算,使庞大的数据先经过初步的整理与呈现,让MES可将运算资源专注于整体产线管理,达到更迅速、更高效的产线制程控制与管理。另外,针对生产操作需求,还可对接不同的上位系统,例如统计制程管制系统 (DIASPC)、配方管理系统 (DIARMS) 等系统全面的整合。
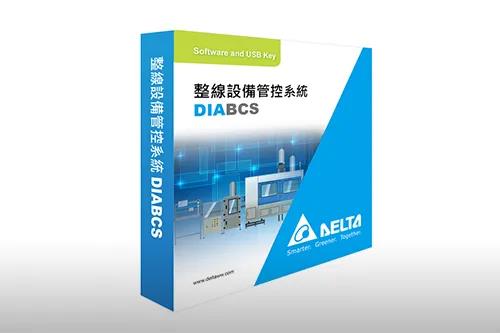
在导入DIABCS整线设备管控系统后,客户产线运行效率有了显著改善。
• 统合通讯模式,规范制造流程:
制定统一通讯规格与一致数据结构,整合80台设备,加快不同设备串联,同时规范设备制造流程、建立设备信息与上位系统通讯。
• 提升产线效率,降低人力成本:
设备模组化,产线建置从以往的5人降至3人即可完成,建置期较快速,另外,无线射频辨识载具管理,搭配RFID / 条码扫读记录生产履历,满足自动及手动过账需求,减少手动刷取条码的人力。
• 自动化与多样性生产:
搭配设备参数设定与设备连线,可自动切换机种生产,并能依据机种判定需使用的物料进行生产,降低人员介入几率与训练时间,达到产线自动化与弹性混线生产需求。
• 产线实时监控与自动备份机制:
通过DIABCS系统固化特征,可在生产过后立即产出对应报表,就算参数变更,也可快速调整与更换。及时收集监控设备状态、同时可追踪并查询异常问题。另外,自动备份机制,主系统发生问题时,自动切换备份系统运作,降低产线停机损失。
台达DIABCS整线设备管控系统,统一设备通讯模式,使设备连接更为顺畅,并通过汇整数据流与边缘计算,降低上位机系统工作负担,达成更迅速、更高效的产线制程控制与管理,使客户的制造生产更灵活、获取监控数据更及时。